THE Manufacturing Toolbox offers Australian manufacturers of all shapes and sizes one of the most comprehensive business capability building resources ever developed.
It does so through the collaboration of its formation partners - the Australian science and research agency CSIRO, QMI Solutions and its subsidiary the Australian Institute for Commercialisation, the Manufacturing On The Move network, Regional Development Australia Brisbane, the Australian Computer Society (ACS), State Library of Queensland, Outsource Institute of Technology, Trade and Investment Queensland, and integrated national media partner, Business Acumen magazine. 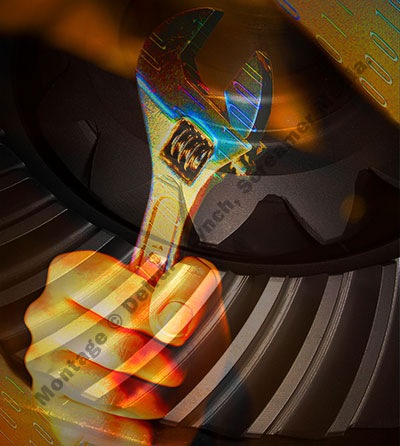
The Manufacturing Toolbox operates as a knowledge resource hub – where business leaders can gather information and inspiration to set their businesses off in new directions. Here they can find experts and best-of-breed services to help achieve their goals.
The Manufacturing Toolbox has been developed over the last 18 months, based on over 15 years of research by Australian company Digital Business insights (DBi) and directly informed and shaped by its collaborative partnerships.
DBi researches and analyses the digital revolution and has surveyed more than 50,000 Australian and multi-national businesses. DBi has conducted in-depth case study analyses on more than 500 organisations and digital entrepreneurs.
Now DBi is turning that research into action through a series of digital business development platforms, the first of which is the Manufacturing Toolbox.
Why the Manufacturing Toolbox?
“Manufacturing is probably the sector most able to understand what the Toolbox offers and derive benefits from it in a short time frame,” DBi chief executive John Sheridan said. “Our work over many years in researching digital disruption and technology adoption has shown us that manufacturers are early adopters of new technologies and they are among the most innovative people in this country.
“We hear in the general media all the time that ‘manufacturing is dead’ in this country,” he said. “Well, our partners in the Manufacturing Toolbox beg to differ.
“Manufacturing in Australia faces great challenges, for certain, but Australian manufacturers bring enormous creativity, resilience and determination to succeeding in their fields. They are among the world’s best innovators – and we believe all they need is some help. 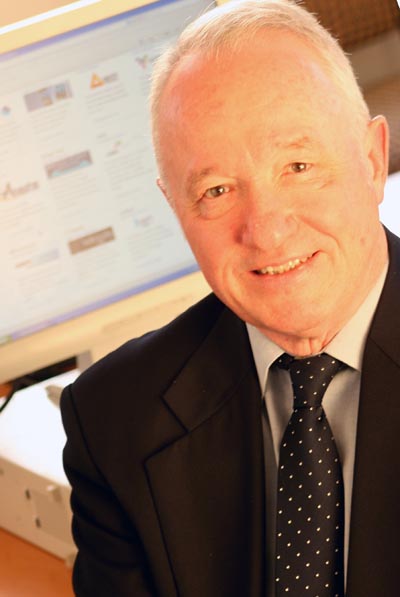
“What the Manufacturing Toolbox does is give manufacturing business leaders information, knowledge, advice – in some cases inspiration – and support networks to help them succeed.
“And beyond that, through our communication and media channels, we offer the great catalyst for success and outreach: targeted information sharing and publicity.”
The networks being brought to the Manufacturing Toolbox by its collaborative partners are extraordinary. CSIRO’s own research and commercialisation is world-leading, and it also provides a conduit to university research.
Australian Computer Society is not only the nation’s most recognised information technology educators and certifiers, it is also exporting those courses and providing Australian-standard qualifications to institutes throughout Asia and the Sub-Continent.
The Outsource Institute of Technology is recognised as a national leader in technology and engineering qualifications, already offering world-leading courses in robotics and 3D printing, among other cutting edge areas of education.
QMI Solutions is probably Australia’s leading technology diffusion organisation and manufacturing educator. QMI Solutions was the first organisation in Australia to use a 3D printer for component prototyping – 20 years ago – and it also pioneered such programs as Lean Manufacturing and Core Value assessments in Australia. Through its Australian Institute for Commercialisation it has also assisted some of Australia’s most successful manufacturers to develop.
The State Library of Queensland offers regional reach to manufacturers and is a learning resource network in its own right. For example, many manufacturers are learning 3D printing techniques through local library courses.
“The Manufacturing Toolbox is a hub where business leaders can learn from people like them who are at the cutting edge,” Mr Sheridan said.
“More importantly, they can then get on and do something about improving their organisation and actively seek out new markets and potential customers. This is the start of something unique. It is the result of an extraordinary collaboration among organisations offering knowledge and their networks with a view to energising manufacturing.
“We hope the Manufacturing Toolbox will help create an unfair advantage for Australian manufacturers – and that’s got to be good for everybody.”
http://manufacturing.digitaltoolbox.org/index.php/uncategorised-publisher/112.
ends