By Mike Sullivan >>
IT IS a business resource centre, a font of information about technologies, a leadership meeting place, a business knowledge hub and – perhaps best of all – a uniquely curated national and international product showcase.
It is the Manufacturing Toolbox – a new and unique digital platform imagined, designed, researched, produced and managed right here in Australia. In less than a month of its soft launch, thousands of business people within Australia and internationally have pored over its stratified, information-rich pages and video clips. 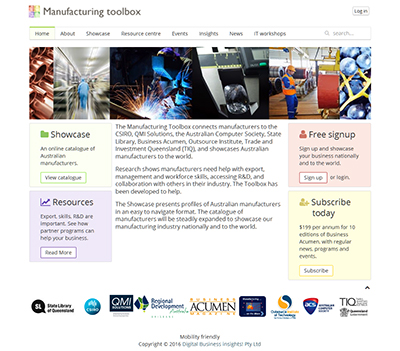
The Manufacturing Toolbox is the first of many custom-designed digital platforms that are emerging from 15 years of research – involving more than 50,000 deep business surveys and case studies focused on business use of technology – by Brisbane-based private company, Digital Business insights (DBi) and industry partners.
These are platforms that are free to join and use – all business leaders and owners have to do is provide some basic information about their companies, and that data is then also used to help shape the content direction of the toolbox.
Once logged in, manufacturers and manufacturing service organisations can add company and product text, images and video to the Showcase section for display. A free monthly e-newsletter is part of the deal.
DBi CEO John Sheridan said the Manufacturing Toolbox was designed to help Australia’s manufacturing business leaders develop their companies, build capability and showcase their products and services to new markets, both local and overseas.
In the case of the Manufacturing Toolbox, key partnerships already include Australian science and research agency CSIRO; QMI Solutions and its subsidiaries the Australian Institute for Commercialisation and ICN; the Manufacturing On The Move network; Regional Development Australia; the Australian Computer Society (ACS); State Library of Queensland; Outsource Institute of Technology; Queensland Trade and Investment; Cook Medical Australia and integrated national media partner, Business Acumen magazine.
The Toolbox is funded and supported by these key partnerships, along with higher subscription levels of access for businesses, ranging from $199 a year to $999 a year for extra levels of showcase content bandwidth, including HD video. The paid subscription options also include a dedicated Manufacturing Acumen e-newsletter along with print and digital subscriptions to Business Acumen magazine.
A unique aspect of the offer is that it provides editorial coverage priority for higher level subscribers.
The Toolbox includes a Resource Centre featuring partner programs, plus video workshops, news, events, insightful blogs from industry experts, and – uniquely – the Showcase of leading Australian manufacturers.
“In the future, we will promote virtual manufacturing trade shows into targeted local and overseas markets, and industry sectors,” Mr Sheridan said. “These will be stand-alone virtual trade shows open for several months at a time and many will coincide with live trade shows, conferences and roadshows in international markets.
“For example, in the case of Taiwan we would establish a virtual Showcase window on Australia’s best-of-breed ICT companies that would be published ahead of, say, a major ICT exhibition and conference,” he said. “That Showcase window would feature companies and products tailored directly for the Taiwan market and its URL would be promoted in the local market by trade and business organisations such as Austrade, Trade and Investment Queensland, the chambers of commerce and others.”
RESOURCE HUB
One of the most popular sections of the Manufacturing Toolbox so far has been the Resource Centre.
Business leaders use the Resource Centre to gather information and inspiration to set their businesses off in new directions. Here they can find experts and best-of-breed services to help achieve their goals.
The Toolbox features hundreds of video presentations to help and improve key aspects of every business, plus problem-solving and forward-looking blogs from industry experts. 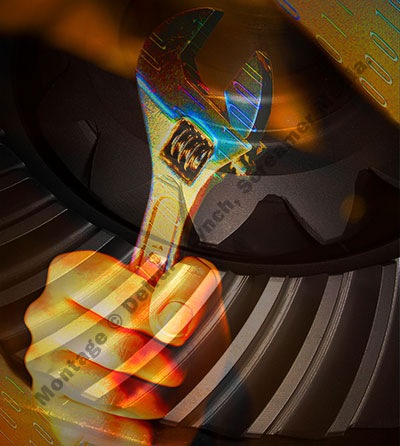
Mr Sheridan said the Manufacturing Toolbox was the obvious place to start for DBi’s digital platforms.
“Manufacturing is probably the sector most able to understand what the Toolbox offers and derive benefits from it in a short time frame,” Mr Sheridan said.
“Our work over many years in researching digital disruption and technology adoption has shown us that manufacturers are early adopters of new technologies and they are among the most innovative people in this country. Now we need to showcase our manufacturers to the world, and that is what the Toolbox is designed to do.
“We hear in the general media all the time that ‘manufacturing is dead’ in this country,” he said. “Well, our partners in the Manufacturing Toolbox beg to differ.
“Manufacturing in Australia faces great challenges, for certain, but Australian manufacturers bring enormous creativity, resilience and determination to succeeding in their fields. They are among the world’s best innovators – and we believe all they need is some help.
“What the Manufacturing Toolbox does is give manufacturing business leaders information, knowledge, advice – in some cases inspiration – and support networks to help them succeed.
“And beyond that, through our communication and media channels, we offer a great catalyst for success and outreach: targeted information sharing and publicity.”
KEY PARTNERSHIPS
The networks being brought to the Manufacturing Toolbox by its collaborative partners are extraordinary.
CSIRO’s own research and commercialisation is world-leading, and it also provides a conduit to university research.
The Outsource Institute of Technology is recognised as a national leader in technology and engineering qualifications, already offering world-leading courses in robotics and 3D printing, among other cutting edge areas of education.
Similarly, ACS is Australia’s foremost provider of training and certification in the ICT sector. So successful has it become in this areA that its programs are already being adopted for certification in several Asian countries.
QMI Solutions is arguably Australia’s leading technology diffusion organisation and manufacturing educator. QMI Solutions was the first organisation in Australia to use a 3D printer for component prototyping – 20 years ago – and it also pioneered such programs as Lean Manufacturing and Core Value assessments in Australia. Through its Australian Institute for Commercialisation it has also assisted some of Australia’s most successful manufacturers to develop.
The State Library of Queensland offers regional reach to manufacturers and is a learning resource network in its own right. For example, many manufacturers are learning 3D printing techniques through local library courses.
“The Manufacturing Toolbox is a hub where business leaders can learn from people like them who are at the cutting edge,” Mr Sheridan said.
“More importantly, they can then get on and do something about improving their organisation and actively seek out new markets and potential customers. This is the start of something unique. It is the result of an extraordinary collaboration among organisations offering knowledge and their networks with a view to energising manufacturing.
“In the trials of the Manufacturing Toolbox, we found most business leaders discovered new information and watched video workshops on the site, then directed their staff and colleagues to those areas which helped to inform discussion and progress new directions for their companies,” he said.
“Apart from the clear marketing advantages offered by the Australian Manufacturing Showcase, trials showed business leaders could use the Toolbox to find and contact best-of-breed organisations and verified experts to assist their companies.
“We hope the Manufacturing Toolbox will help create an unfair advantage for Australian manufacturers – and that’s got to be good for everybody.”
http://manufacturing.digitaltoolbox.org
ends